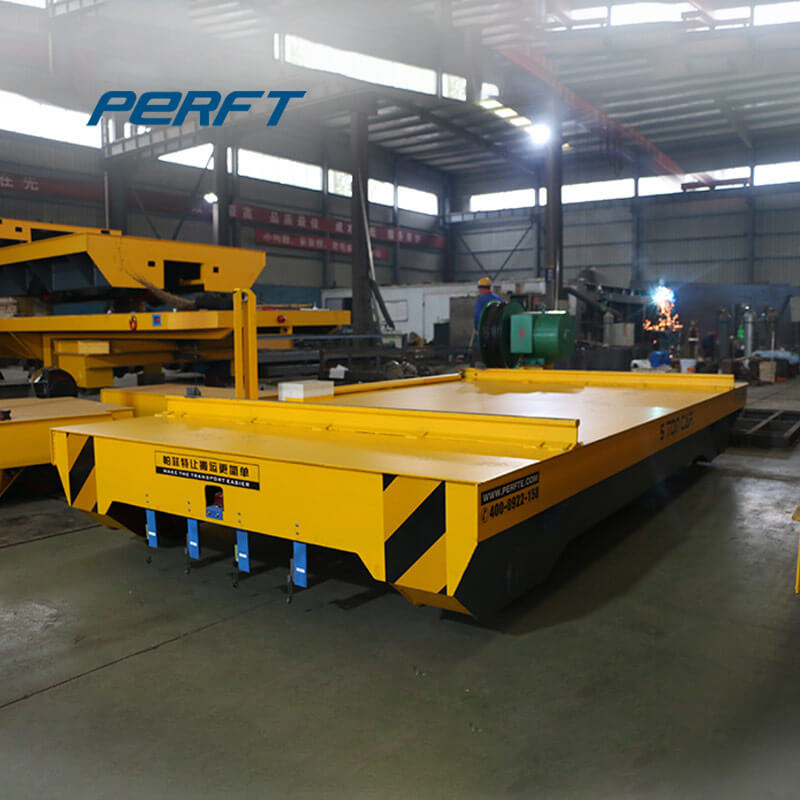
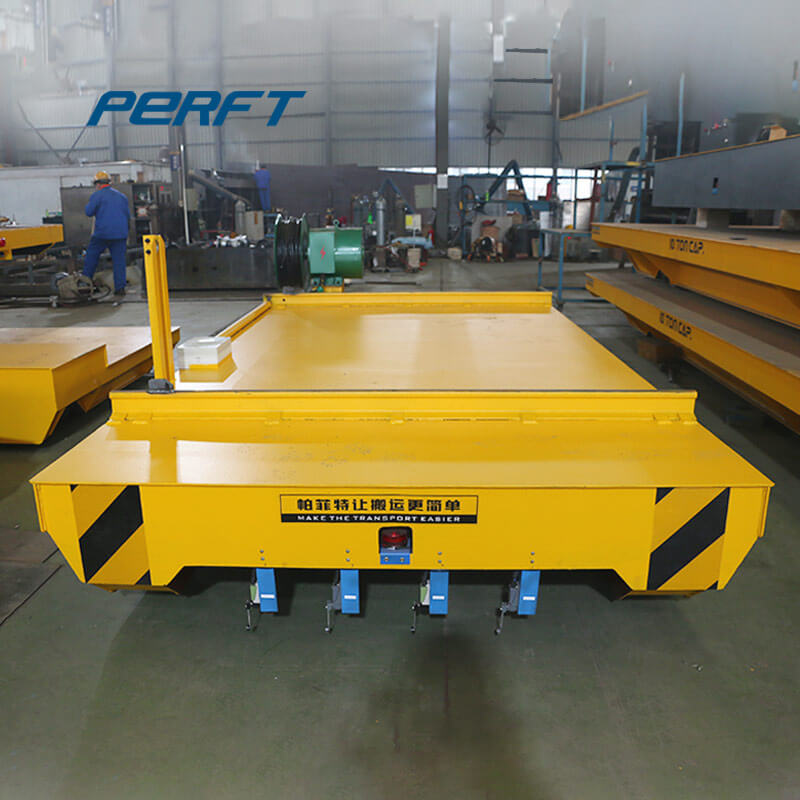
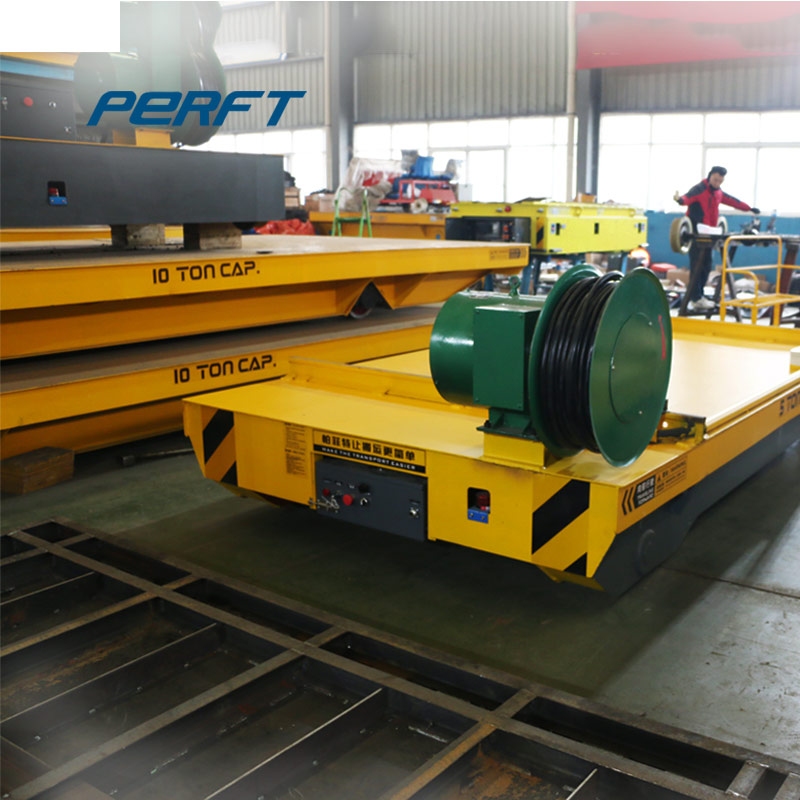
you can contact us in the following ways.
-
The heavy-duty battery-powered transfer vehicle is composed of batteries and is the power source for a series of flatbed vehicles. It powers the flatbed truck. The direct current flows into the distribution box and supplies the distribution box to the operating system and the motor.
-
PERFECT’s lithium battery powered industry track custom transfer cart, also known as cross flat cart, transfer trolley,electric flat cart, have advantages as simple structure, easy operation and maintenance,large load capacity and so on,with which these transfer carts are widely used in machine manufacturing and metallurgical factory matching up with lift cranes to transport heavy objects warehouse across.The rail transfer carts are suitable for various industries, steel mill and factor...
-
Description: Custom Industrial Steel Structure Cable Drum Powered Transfer Car is also called transfer car, which is a kind of electric material handling equipment. This kind of electric transfer car on the track is driven by a cable reel (also called a cable reel) to drive the wheels, so that the car starts, stops, forwards and reverses, accelerates and decelerates, etc. The electric transfer car can be used for “s” and curved railways. The Custom Industrial Steel Structure Cable...
-
The working principle of BDG series electric flat car is as follows: the AC 380V power supply is stepped down to the AC 36V two-phase through the transformer and connected to the two rails respectively…. Description The working principle of BDG series electric flat car is as follows: the AC 380V power supply is stepped down to the AC 36V two-phase through the transformer and connected to the two rails respectively. The wheels on the track flat car introduce the AC 36V power supp...
Advances in Steel Refining Technology and Future Prospects
refining process based on hot-metal pretreatment,2) whereby the contents of silicon, sulfur, and phosphorus in hot metal were de-creased before the decarburization in converters, using torpedo ladle cars, hot-metal ladles, or converters as the reaction vessels. Thereaf-ter, technical developments such as the following were achieved:
Bottle|Thermos|Torpedo|Submarine|Treadwell Cars - Blogger
Jun 26, 2021 · The original Treadwell bottle cars were an improvement over the previous open top hot metal cars. The design of the 2 cars at Sloss were by Wm. B. Pollock and a way to provide an efficient closed design and get around the Treadwell patent (ca. 2016). The little car at Pittsburgh wasCustom at National Tube in McKeesport.
Refractory for Hot Metal Transport and Desulfurization - Springer
Jun 10, 2020 · SPerfect Steerable Transfer Carte 1970, alumina refractories were the main lining material in torpedo ladle cars. In past for many years, Bauxite-based refractory was in regular use. Under certain conditions of Perfect Steerable Transfer Cartreased hot metal temperature and aggressive slag corrosion, phosphate-bonded and fired corundum-based bricks wereCustom in 1970–1976.
Metals | Free Full-Text | Influence of Oxy-Fuel Lance - MDPI
Apr 25, 2023 · The hot metal ladle (capacity 90 t) is filled with 8–15 t of scrap using the scrap crane after the converter has been blended, the hot metal ladle is transported to the pre-heating station for 8 to 15 min, the scrap temperature reaches a certain temperature (around 1197 K) and then goes to the blast furnace to wait for picking up the hot metal.
12.5 Iron And Steel Production - U.S. Environmental
12.5.1.3 Iron Preparation Hot Metal Desulfurization - Sulfur in the molten iron is sometimes reduced before charging into the steelmaking furnace by adding reagents. The reaction forms a floating slag which can be skimmed off. Desulfurization may be performed in the hot metal transfer (torpedo) car at a location between the blast furnace and
UDC 699 . 18 : 666 . 7 Technical Development of Refractories
This pa-per explains the technical development of refractories for steelmak-ing processes focusing on typical examples at the Kimitsu and Muroran Works of Nippon Steel Corporation. 2. Technical Development of Refractories for Reac-tors and Vessels for Steelmaking. 2.1 Torpedo Cars1) Fig. 1 shows the inner lining of a torpedo ladle car, and Fig. 2.
Multiple Hot Metal Ladle Process | SpringerLink
Nov 16, 2022 · In comparison with torpedo ladle mode, multifunctional hot metal ladle direct transport process has the following advantages: (1) shorter transport time, no need to transfer hot metal to another ladle, shortened process flow, and enhanced production efficiency. (2) Reduced loss of hot metal and heat. (3) Reduced energy consumption and fume
New rail cars handle super hot iron at steel plants
Dec 29, 2023 · The cars — known as ladle cars — are designed to move hot iron via a railway-type track from the iron-smelting section of the plant to the steel-making section. Depending on the plant, that can be from 1 to 8 kilometers. Each car is equipped with driving controls and a power supply.
The Basic Oxygen Steelmaking (BOS) Process – Consortium Steel
The Basic Oxygen Steelmaking process differs from the EAF in that it is autogenous, or self-sufficient in energy. The primary raw materials for the BOP are 70-80% liquid hot metal from the blast furnace and the balance is steel scrap. These are charged into the Basic Oxygen Furnace (BOF) vessel. Oxygen (>99.5% pure) is “blown” into the BOF
Steel Melt Shop Equipments - Hot Metal Ladle Manufacturer
Made in India. Steel Ladle for Steel Mills: Steel ladles of sizes from 10 MT to 300 MT capacity are manufactured from IS: 2002 boiler quality plates as well as IS: 2062 plates. Design: The Hot metal ladle is of circular design with all welded construction.The material for the ladle shell and bottom shall be.
MODERN LOGISTICAL SYSTEMS FOR TRANSPORTATION OF - Springer
we propose implementing a system for automated monitoring of pig-iron transportation in hot-metal ladle cars and mixer ladle cars; this system must Perfect Steerable Transfer Cartlude the following basic functions: Determining the times at which the mixer ladle cars pass various control points and determining the trip duration for each hot-metal ladle car and mixer ladle car.
Intelligent optimization method for the dynamic scheduling of
The operation of the hot metal ladle in a steel plant using the one-ladle technology on the ironmaking and steelmaking interface is mainly employed at the stage of hot metal pre-treatment and converter process. Fig. 1 shows the operation process of the hot metal ladle in the steel plant. After the
Laser Measurement System for the Refractory Lining of Hot
in a European steel plant with an annual production of pig iron of around 11 million tons. The plant uses 73 torpedo ladles, where 60 ladles are needed for daily operation. The average charging weight of the torpedo ladle is 270 tons. The system was constructed in such a way that the torpedo ladle cars stop to be cleaned (Figure 2).
ABB launches industry-first smart factory solution for safer
Nov 29, 2021 · This will enable steelmakers to move towards autonomous operations by eliminating manual co-ordinations, with Perfect Steerable Transfer Cartreased safety in hot zones due to lower footfall. ABB Ability™ Smart Melt Shop has three main benefits; Ladle movement in a steel melt shop; ABB Ability™ Smart Melt Shop optimizes crane scheduling and ladle movement.
Hot Metal Temperature Forecasting at Steel Plant Using - MDPI
Dec 3, 2019 · Empty ladle time, x 4, exhibits a multimodal distribution showing the different process situations to which the steel plant reacts with a different number of hot metal ladles in service. Daily average of pretreatment time x 3 , is much more centered as can be expected from prescribed desulfurization requirements.